For Original Equipment Manufacturers (OEMs), selecting the right heat sink manufacturer is a crucial decision that directly impacts the performance, reliability, and overall success of their products. A subpar heat sink can lead to overheating, system failures, and ultimately, dissatisfied customers. Partnering with a reputable and experienced heat sink manufacturer is essential for ensuring optimal thermal management solutions tailored to your specific needs. This guide will outline the critical factors to consider when choosing a heat sink supplier, the importance of material selection in Extruded Heatsink manufacturing, and the significance of quality assurance standards in professional heat sink production.
Table of contents:
5 Critical Factors to Evaluate When Choosing a Heatsink Supplier
The Role of Material Selection in Extruded Heatsink Manufacturing
Quality Assurance Standards in Professional Heat Sink Production
5 Critical Factors to Evaluate When Choosing a Heatsink Supplier
Choosing the right heat sink manufacturer requires careful evaluation based on several key factors. First, assess the manufacturer's experience and expertise. Look for a company with a proven track record of designing and manufacturing high-quality heat sinks for diverse applications. Check their portfolio and client testimonials to gauge their capabilities. Second, consider their manufacturing capabilities and equipment. Do they possess the necessary machinery and expertise to handle your project's specific requirements, including Extruded Heatsink production, CNC machining, and surface finishing? Third, evaluate their design and engineering support. A good manufacturer should offer comprehensive design assistance and be able to optimize your heat sink design for maximum thermal performance and cost-effectiveness. Fourth, examine their quality control processes and certifications. Ensure they adhere to rigorous quality standards and possess relevant certifications like ISO 9001. Finally, consider their pricing and lead times. Obtain quotes from multiple manufacturers and compare their pricing structures and lead times to ensure they align with your budget and project timeline.
The Role of Material Selection in Extruded Heatsink Manufacturing
Material selection plays a critical role in the performance and cost-effectiveness of Extruded Heatsink manufacturing. Aluminum is the most commonly used material due to its excellent thermal conductivity, lightweight properties, and cost-effectiveness. Different aluminum alloys offer varying levels of thermal performance and mechanical strength. For example, AL6063 is a popular choice for its good thermal conductivity and machinability. Copper, while offering superior thermal performance, is heavier and more expensive, making it suitable for applications with stringent thermal requirements where cost is less of a concern. The choice of material should be based on a careful evaluation of the heat sink's application, thermal requirements, weight constraints, and budget. A skilled heat sink manufacturer can provide expert guidance on material selection to optimize performance and minimize costs.
Quality Assurance Standards in Professional Heat Sink Production
Rigorous quality assurance standards are essential for ensuring the reliability and performance of heat sinks. A reputable heat sink manufacturer should implement comprehensive quality control processes throughout the entire production cycle, from material sourcing to final inspection. This includes dimensional inspections, thermal performance testing, and visual inspections to identify any defects or deviations from specifications. Adherence to industry standards such as ISO 9001 demonstrates a commitment to quality and ensures that heat sinks are manufactured to the highest standards. Statistical Process Control (SPC) techniques can also be used to monitor and control the manufacturing process, minimizing variations and ensuring consistent quality. By prioritizing quality assurance, manufacturers can minimize the risk of defects and ensure that heat sinks meet the demanding requirements of OEM applications. Working with a manufacturer that prioritizes quality, like Renxin Precision, ensures you receive reliable and high-performing components.
In conclusion, selecting the right heat sink manufacturer is a critical decision for OEMs. By carefully evaluating factors such as experience, manufacturing capabilities, design support, quality control, and pricing, you can find a partner that meets your specific needs and ensures the success of your products. Prioritizing material selection and rigorous quality assurance standards in Extruded Heatsink manufacturing is essential for achieving optimal thermal performance and reliability. Partnering with a reputable and experienced manufacturer will ultimately lead to superior heat sink solutions and increased customer satisfaction.
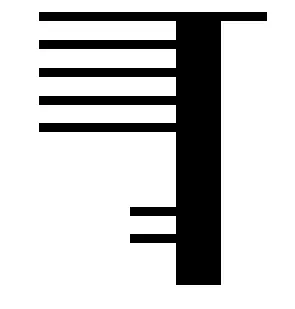
Comments
Post a Comment