Table of content:
What Makes CNC Lathe Machining Parts Core to CNC Product Offerings
Key Components of CNC Lathe Parts: Chucks, Turrets, and Control Panels
Why Precision Controls Surface Finish in CNC Lathe-Produced Parts
What Makes CNC Lathe Machining Parts Core to CNC Product Offerings
CNC lathe machining parts are essential to manufacturing, offering versatility and precision. Unlike traditional methods, CNC lathes produce complex geometries with tolerances in the thousandths of an inch. These parts transform raw materials into precise components, meeting exact specifications. The automated process ensures consistent results across large production runs, making them invaluable for companies needing reliable wholesale solutions. Professional suppliers like Zhichuanglian know the quality of these parts directly affects the entire production chain. Sourcing wholesale CNC lathe parts means access to rigorously tested components that meet industrial standards. Beyond cost savings, superior parts reduce downtime, minimize waste, and speed up production cycles—key advantages in competitive markets. Modern CNC lathe parts also feature advanced materials and coatings, extending their service life and providing long-term value.
Key Components of CNC Lathe Parts: Chucks, Turrets, and Control Panels
The performance of a CNC lathe relies on three key components working together to deliver precise results. Chucks, the primary workholding mechanism, secure materials during machining. High-quality chucks use precision-ground jaws to evenly distribute clamping forces, preventing distortion and maintaining concentricity. Modern designs with quick-change capabilities reduce setup times and boost productivity. Turrets, the second essential component, house multiple cutting tools in a rotating assembly for rapid, automated tool changes. Advanced systems can hold dozens of tools, from rough turning inserts to precision boring bars, all positioned with micron-level repeatability. Their precise indexing ensures tools return to exact positions, maintaining accuracy over long production runs. Control panels act as the operation’s brain, featuring intuitive interfaces for programming complex machining sequences. Modern systems enable real-time monitoring, predictive maintenance alerts, and integration with manufacturing execution systems. They process thousands of calculations per second, optimizing spindle speeds, feed rates, and tool paths. Together, these components enhance each other, enabling CNC lathes to consistently produce precise, reliable parts that meet or exceed industry standards.
Why Precision Controls Surface Finish in CNC Lathe-Produced Parts
Surface finish quality in CNC lathe machining directly depends on the precision of control systems managing the cutting process. Modern CNC controllers use advanced algorithms to monitor cutting forces, tool wear, and thermal conditions in real time, making micro-adjustments to maintain optimal surface conditions. Key factors include spindle speed stability, feed rate consistency, and tool path accuracy. Advanced manufacturers use closed-loop feedback systems to compare actual performance with programmed parameters, correcting deviations before they affect surface quality. Vibration-dampening technologies eliminate resonances that can cause surface irregularities or dimensional errors, while temperature compensation algorithms ensure stability by accounting for thermal expansion. Precision systems also manage coolant flow and pressure, optimizing chip removal and maintaining tool life and surface integrity. When sourcing CNC lathe parts from manufacturers like Zhichuanglian, customers benefit from these advanced technologies, resulting in parts with exceptional surface finishes that often eliminate the need for secondary operations. This is crucial for applications like sealing surfaces, bearing races, or optical components, where surface finish directly impacts performance.
Success in modern manufacturing relies on working with CNC lathe machining parts manufacturers who understand both technical needs and business goals. Companies like Zhichuanglian offer decades of CNC machining expertise, providing solutions beyond basic part production. Partnering with experienced manufacturers gives you access to engineering advice, material recommendations, and process improvements that boost quality and cut costs. The best manufacturers focus on continuous improvement, updating equipment and training regularly to stay ahead in the industry. When evaluating potential partners for wholesale CNC lathe machining parts, consider their commitment to quality certifications, delivery reliability, and technical support capabilities that ensure long-term success for your manufacturing operations.
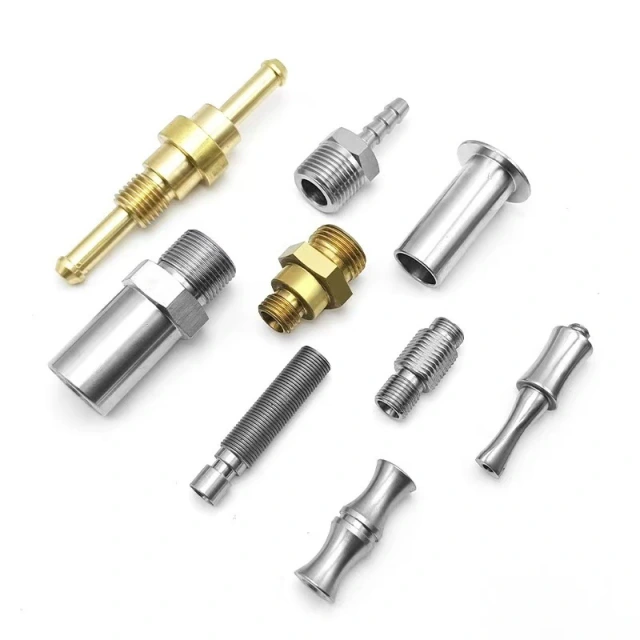
Comments
Post a Comment