Table of contents:
Step-by-Step Production Process of a Private-Label Cushion Foundation
Key Checkpoints in Quality Control During Cushion Manufacturing
Step-by-Step Production Process of a Private-Label Cushion Foundation
The development of a custom cushion foundation begins with market research and conceptualization. Manufacturers assess industry trends, customer preferences, and gaps in the market to craft a product that stands out. Once the concept is finalized, the formulation process begins, focusing on high-performing ingredients to ensure smooth application, long-lasting wear, and skin benefits. The liquid formula is meticulously combined with pigments, moisturizers, and active ingredients to strike the perfect balance of coverage and wearability. From here, the liquid product is infused into cushion pads, which hold and release the product evenly for seamless application.Packaging selection is the next step, where the focus shifts to innovative design and materials. Customization of the compact, mesh tops, and accompanying applicators ensures a cohesive and attractive final product. During the manufacturing phase, rigorous testing is conducted to ensure compliance with safety standards, efficacy, and consistency. This involves validating the formula's performance under various conditions and ensuring the durability of the compact and mesh. Finally, the product is assembled, packaged, and prepared for shipment to storefronts or directly to customers.
Choosing the Right Formula
One of the most appealing aspects of custom cushion foundations is the flexibility to select the perfect formula. Whether your goal is a radiant glow, a matte finish, or skincare-enhanced foundation, there’s a solution to fit every need. Glow formulas prioritize a dewy and luminous look, often infused with hydrating ingredients such as hyaluronic acid or Damask rose water to lock in moisture. On the other hand, matte cushions cater to those desiring oil control and a shine-free appearance. These are enriched with ingredients such as sebum-reducing powders to achieve a flawless matte effect. For those in favor of multi-purpose products, skincare-infused cushions offer a mix of active ingredients including SPF, antioxidants, and botanicals, combining makeup with skincare benefits. Brands like the Clio Kill Cover Mesh Glow Cushion, for example, excel in offering a radiant glow while providing notable skin hydration through ingredients like chamomile and hyaluronic acid. With such versatility, selecting the right formula ensures the foundation delivers flawless coverage while supporting individualized skincare needs.
Packaging Customization
A key aspect of custom cushion foundations lies in their packaging, which is not merely aesthetic but also functional. Packaging plays an essential role in maintaining product integrity and delivering a premium user experience. Designing mesh tops is a priority, as these not only assist with even product application but also prevent excess product release, enabling users to achieve buildable coverage without waste. Compact designs offer endless creative opportunities to align the product with brand identity. Packaging can range from sleek minimalist finishes to vibrantly branded options featuring custom logos and prints.Whatever the design, thoughtful packaging ensures usability and enhances the product's appeal, making it stand out on the shelf.
Key Checkpoints in Quality Control During Cushion Manufacturing
When manufacturing custom cushion foundations, maintaining stringent quality checks at every stage is essential to create a reliable and high-quality product. From formulation to packaging, each element undergoes thorough inspection. The formula is meticulously tested for consistency, texture, and adherence to desired performance properties, including coverage, longevity, and hydration levels. Packaging quality is evaluated through durability tests, ensuring that the compact withstands wear and tear. Ensuring the secure fit of the cushion, mesh, and closures prevents leaks and maintains product integrity. Once assembled, the product undergoes final inspections, including thermal and drop tests, to verify that both the formula and packaging remain unaffected under various circumstances. Approval from regulatory bodies is the final step, certifying the product complies with industry standards for safety and efficacy.
The meticulous process of designing, testing, and assembling the product ensures a balance between functionality, durability, and safety. Each stage, from material selection to final inspections, plays a critical role in delivering a high-quality product that meets both customer expectations and regulatory standards. By prioritizing attention to detail and rigorous testing methods, we ensure the final product embodies reliability and excellence, ready to meet the diverse needs of consumers.
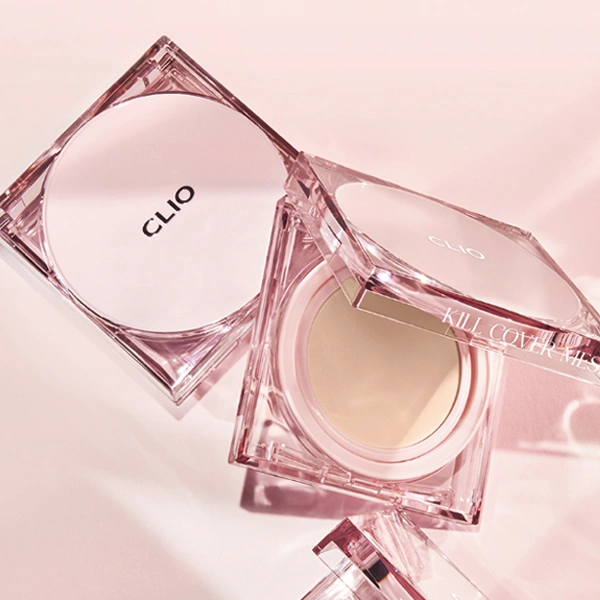
Comments
Post a Comment